Established process
At this company, all records of most parts of the manufacturing process were made and kept offline. This was necessary for security but limited efficiency by a great deal.
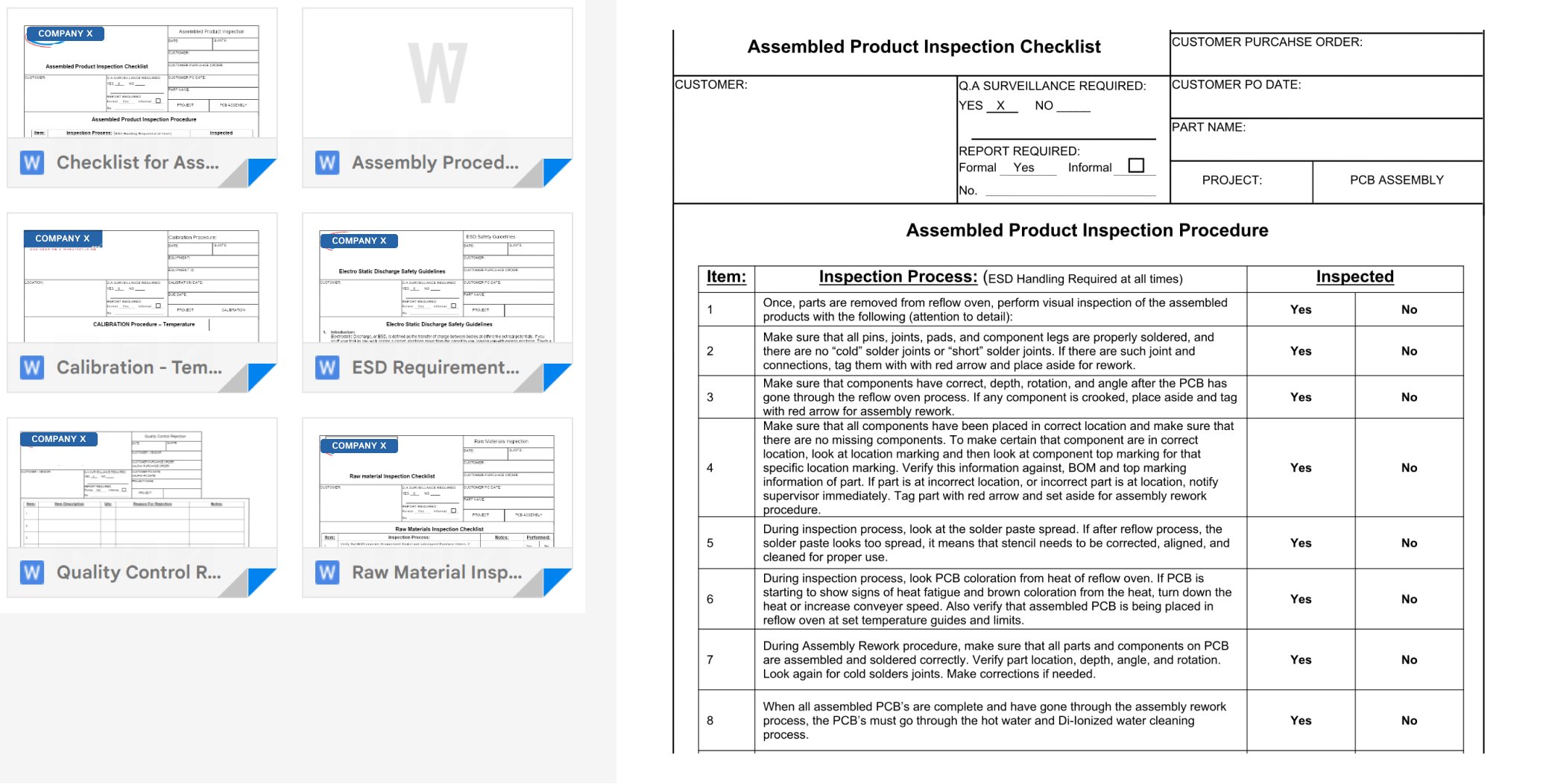
Samples of the documents that kept records of each step of the manufacturing process at this company.
Mapping out
With knowledge gained from user research and discussions with the stakeholders, I set out to create a detailed map of the information architecture. From this exercise, I was able to determine three overall modules the software would have: Inventory, Manufacturing, Quality Management. By analyzing the necessary functions of each of those modules, I mapped out all the pages that would be necessary underneath those.
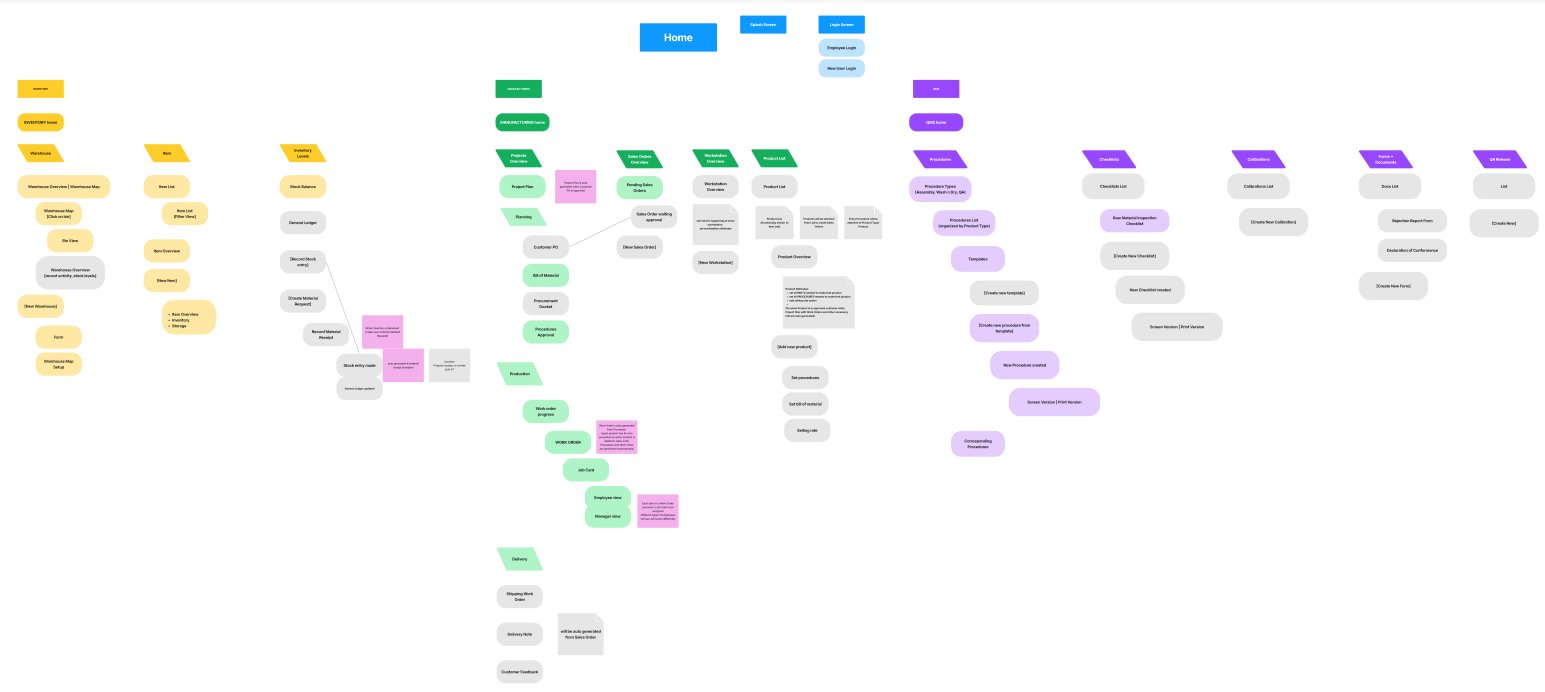
I iterated upon this, meeting with the stakeholders to confirm that the architecture did align with the established processes.
Design System
After creating the User flow, I started working on creating the smaller components of the design system, such as clickable elements and section headings.
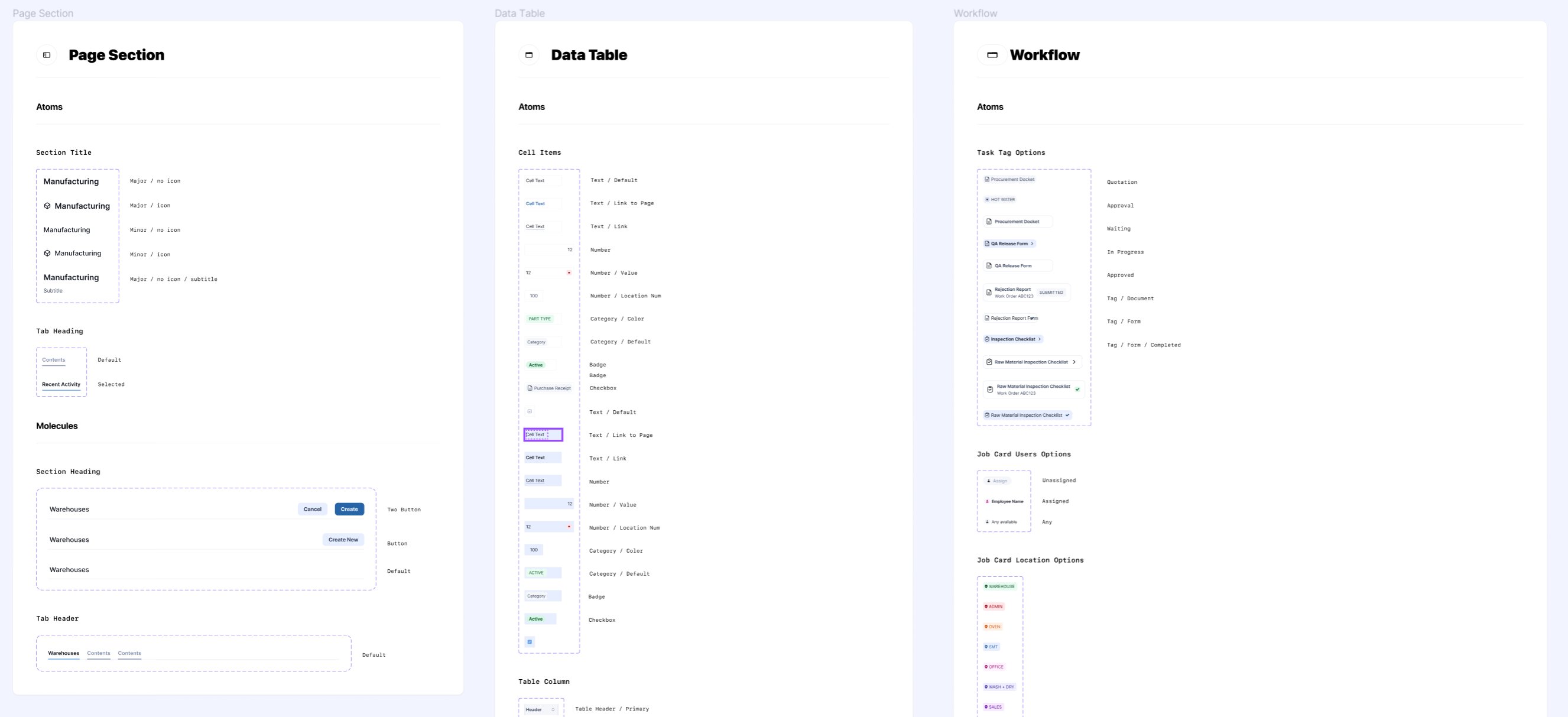